Introduction:
Valves are essential parts in a variety of applications, including power plants, water systems, and more. When it comes to controlling fluid or gas flow in a piping system, choosing the appropriate valve is critical. Angle valves and ball valves represent two widely used options, each offering unique strengths and considerations. In this guide, we will delve into the features, performance considerations, and factors to help you make an informed decision. Whether you are working on a plumbing project or managing an industrial facility, understanding the differences between angle valves and ball valves is essential.
What is an Angle Valve?
An angle valve is a versatile tool commonly employed in plumbing applications. It offers efficient water flow regulation in piping systems. Commercial settings, including chemical manufacturing facilities, also utilize angle valves. Manufacturers construct these valves with durable materials to withstand various operating conditions and ensure reliable performance.
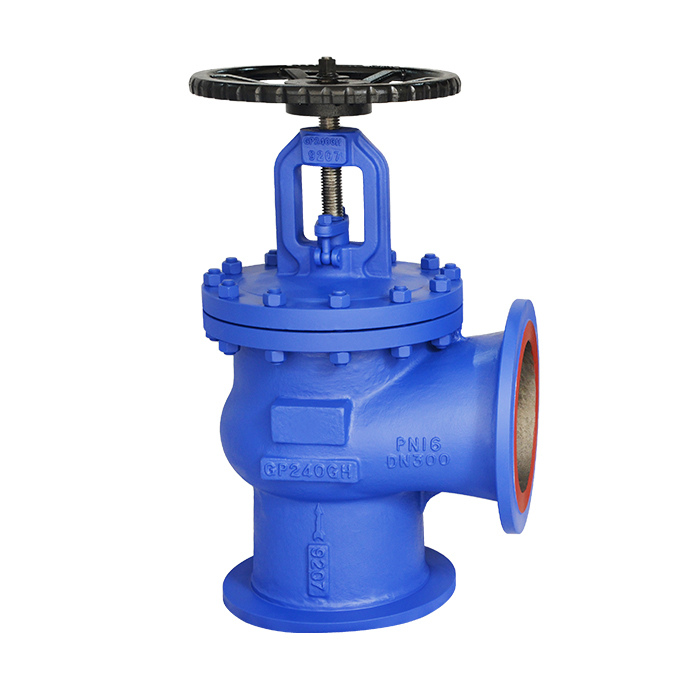
1. Image of an Angle Valve
What is a Ball Valve?
A ball valve is a highly versatile valve type that utilizes a spherical disk to control fluid flow. They find extensive usage in water and gas pipelines, oil pipelines, and chemical processing facilities. With its unique design, it enables easy operation and reliable shut-off capabilities. Opening the valve involves rotating the disk perpendicular to the aperture, allowing fluid to pass through. Conversely, closing the valve aligns the disk parallel to the opening, effectively stopping fluid flow.
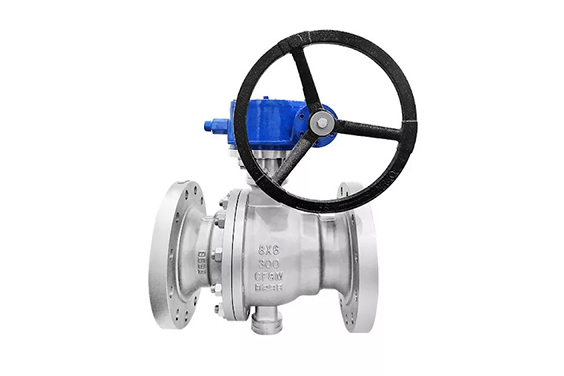
2. Image of a Ball valve
Factors to Consider:
- Performance Requirements: Consider the characteristics of the conveyed media, such as corrosiveness or high-pressure and high-temperature conditions. In demanding applications, specialized valves or alternative materials may be necessary to ensure optimal performance and durability.
- Port Configuration: Evaluate the available space and plumbing restrictions to determine the most suitable valve type. If space is limited, opting for a ball valve might be the preferred choice. Additionally, consider whether the pipe connections allow for the installation of the desired valve type.
- Exposure Situations: Assess the anticipated service life of the valve in relation to factors such as vibration, abrasive media, shock loads, and heat cycles. These environmental conditions can impact the valve’s durability and reliability. Selecting the appropriate valve type can help mitigate potential issues.
- Maximum Flow Rate (Qmax): Determine the maximum flow rate that the valve needs to handle under typical inlet pressure and temperature conditions. Ensure that the selected valve is capable of effectively managing the required flow rate.
- Operating Cost: Consider the frequency of valve usage and its impact on operating expenses. Angle valves offer the advantage of being closed without the need for full rotation off the seat, reducing strain on internal parts. However, it’s important to note that both angle valves and ball valves can experience corrosion and leakage if not properly maintained.
To get further information on industrial valves and make the right selection for your specific requirements, contact us at sales@knotsandgear.com
4 Responses
I like it when people get together and share views. Great site,
stick with it!
Thank you
Hi my friend! I want to say that this article is
awesome, nice written and come with almost all significant
infos. I would like to look extra posts like this .
Thank you